Mining the Future
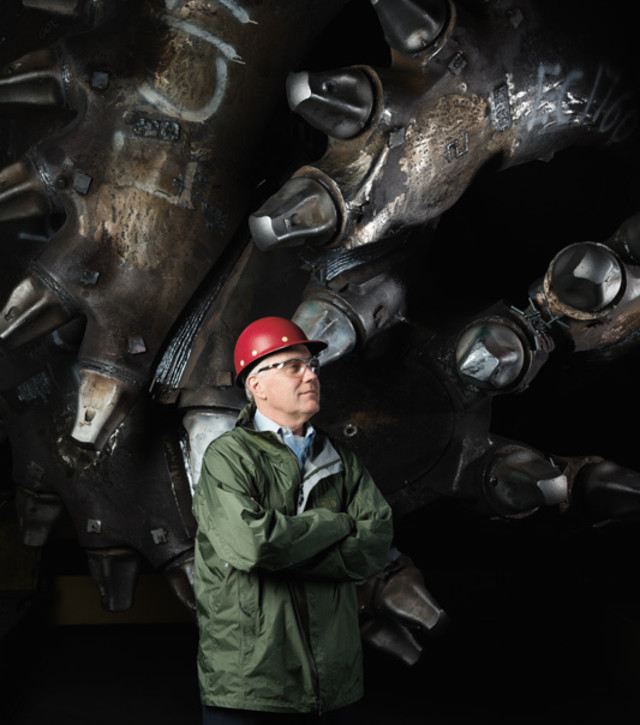
Image: Michael Schmitt
A few blocks from patrons munching St. Honoré pastries near the tree-lined calm of upper NW 23rd Avenue, Esco vice president of engineering John Dillon watches an arc furnace heat nine tons of steel to 3,000 degrees. As one worker checks the steel’s temperature with a long thermometer, another cranks a wheel that tips the whole furnace over a gigantic bucket. White-hot metal pours out, as fluid as water.
“I never get tired of seeing that,” says Dillon, 59, as a crane hoists the giant bucket of white-hot steel. “There’s a reason I’ve been here 33 years. I have a cool job.”
As head of Esco’s 80-employee engineering division, Dillon is key to one of Portland’s most undersung industrial dynamos. Esco, founded in 1913, makes “wear” parts for big mining tools—the replaceable components that attach to diggers, drills, and scoops, all designed to munch through rock. According to Dillon, some of Esco’s steel parts last weeks or months. Others must be replaced after just hours.
“It’s a razor/razorblade thing,” says the Eastern Washington native. “You want to have the razor, of course. But you’re really interested in selling the blade.”
Esco has had just seven CEOs in 100 years. “There’s a big family element,” Dillon says.
Esco sells a lot of razor blades. The company’s worldwide headquarters in Portland pours and ships more than 130,000 pieces of gear every month, with more than $1 billion in annual revenue. (Esco has been in the preliminary stages of going public since 2011.) A metallurgist by training, Dillon designs equipment crucial to some of the world’s most complex (and sometimes controversial) projects. The company builds parts for dozers and excavators working the Canadian oil sands and recently produced room-sized cutters to gouge out an expansion of the Panama Canal.
Dillon’s team designs machines with esoteric names: Posilok Plus, SV2, Ultralok. But their success has real implications on the street. In a world in which the iPhone in your pocket can exist only because of complex mining operations, even the smallest efficiencies can mean huge profits for Esco’s clients. Earlier this year, Dillon and his crew received a prestigious Mining Magazine award for the Nemisys system, a steel lip that attaches to bulldozer buckets, allowing for quicker and safer mining.
“We don’t have Intel’s cachet,” says Dillon, “but our engineers face real challenges.”