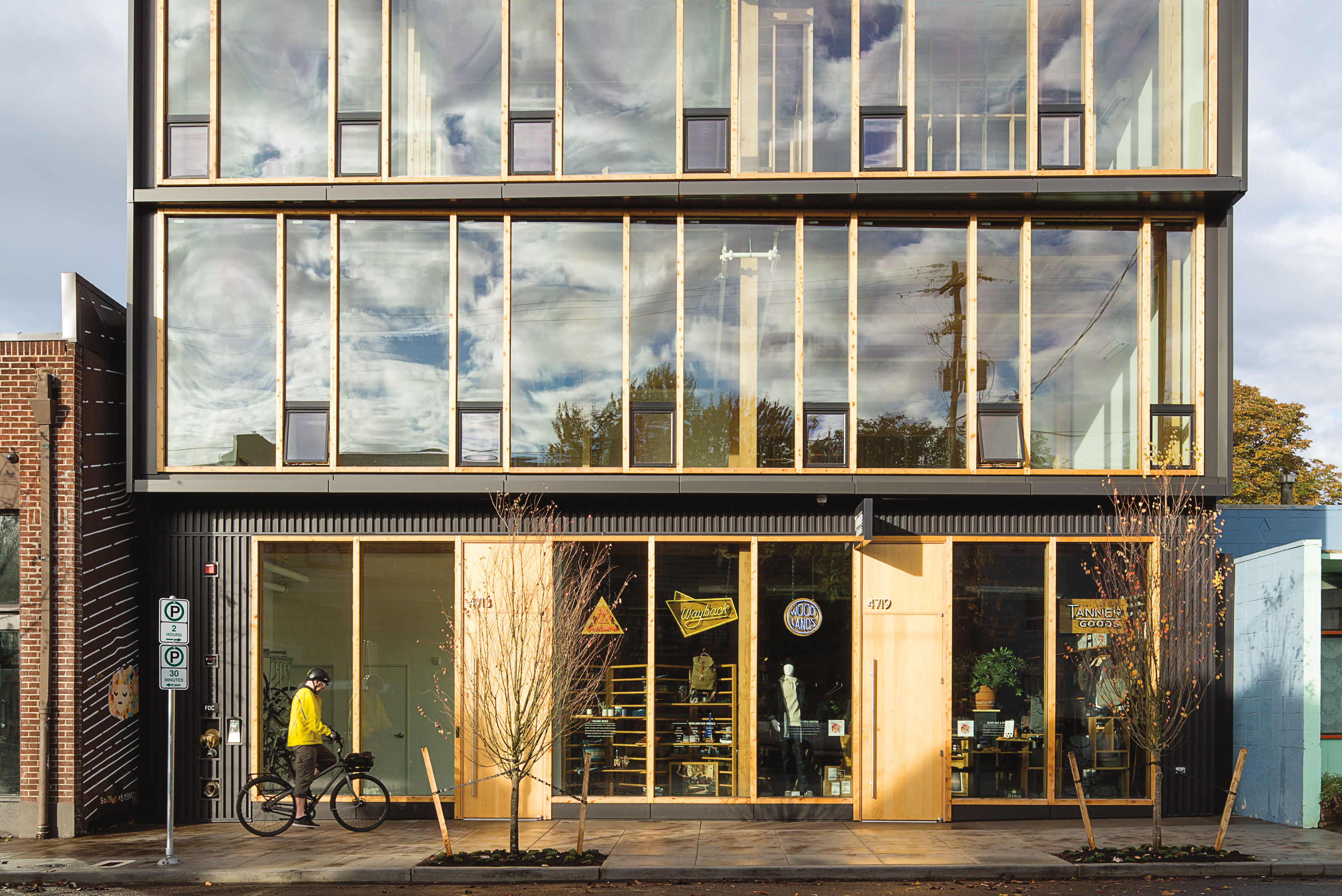
The Future of Portland's Skyline Is Made of Wood. Yes, Wood.
High-rise construction sites don’t usually smell particularly good. But this winter, at the nearly finished building called Carbon12 at the corner of North Williams and Fremont, a resinous, boreal aroma exuded from more than 290 tons of Doug fir, spruce, and pine that will frame the building’s eight stories.
Redevelopment has transformed that east-side intersection and its neighborhood in recent years. New multistory, mixed-use buildings now march along, flanking busy car, bike, and bus traffic on Williams. The woodsy aura, however, marks the 85-foot-tall Carbon12 as something different, arguably even revolutionary: part of a new generation of timber-based structures that promise a more sustainable, seismically resilient way to build—and a new economic catalyst for Oregon, a state split between booming, rebuilding Portland and stagnating rural timber towns.
“The building isn’t even done yet, but it’s getting toured probably two or three times a week,” says Ben Kaiser, whose companies, Kaiser Group and PATH Architecture, developed and designed the project. “Which is exactly what we wanted.”
As we walked the site, the sounds of sawing and hammering were notably absent. Panels of cross-laminated timber, the technology at the heart of Carbon12, are manufactured elsewhere and simply craned and fastened into place. Even so, Kaiser says the project hasn’t been easy.
“We really have forgotten how to build with wood,” he says. “We’re all kind of learning again.”
Four years ago Kaiser, who already had a long track record as a developer in North and Northeast Portland, visited the Bullitt Center in Seattle, the first commercial structure in America to meet a stringent set of energy and environmental guidelines known as the Living Building Challenge. Besides its solar power and Thermos-like insulation, the Bullitt has a structural framework of timber rather than steel, vastly reducing the building’s carbon footprint.
“I came home and said to myself, ‘Everything I do in the future will be changed,’” remembers Kaiser, now 50. His Radiator Building, near Carbon12, became Portland’s first large timber-framed structure in generations. Other developers and designers followed. The Framework building in the Central Eastside soon arrived, as did Albina Yard in North Portland and 38 Davis in Old Town.
“Right here is the biggest concentration of timber buildings in the US,” Kaiser says. Carbon12’s shape, with a deep cut in the façade bringing light into the interior, takes inspiration from a nurse log: a fallen tree that becomes a host for a new seedling. “We’re fostering new growth in the same way,” he adds. “This is going to be the next 25 years of architecture. And Portland is the leader.”
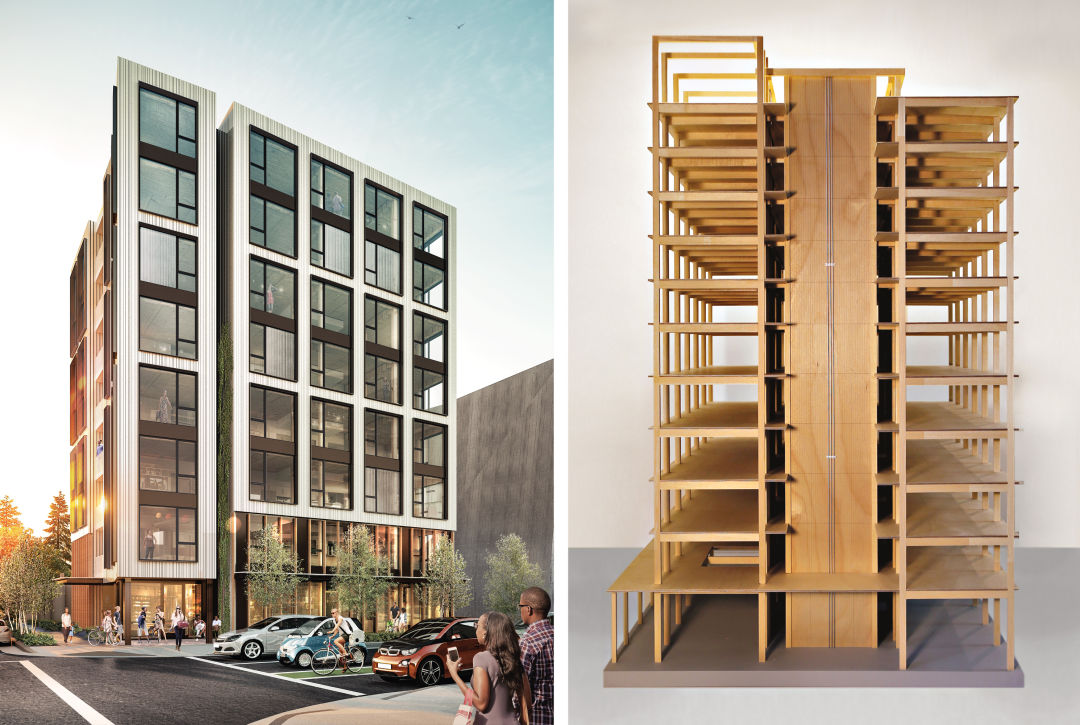
From left: a rendering of Carbon12; a mock-up of Framework, Lever's forthcoming Pearl District high-rise
Image: Courtesy Lever Architecture and Courtesy Kaiser Group
For thousands of years, people built with wood. But with the Industrial Revolution came steel, strong enough to support skyscrapers.
Starting in Austria about 20 years ago, however, two technical advances allowed stronger, taller wood buildings than ever before—even skyscrapers. For one, engineers improved structural connections between walls and floors, making timber-framed buildings better able to withstand earthquakes. More significantly for Oregon’s emerging generation of wood buildings, builders began using cross-laminated timber, or CLT: manufactured panels created by gluing together layers of wood, then compressing them into a packed structure as strong, pound for pound, as steel—construction-wise, a kind of Holy Grail with splinters. CLT is strong enough to replace steel or concrete as the main structural element of high-rise buildings—meaning that big things can be built from renewable trees that suck carbon out of the atmosphere and store it, instead of smelted iron ore or concrete, the production of which entails huge carbon emissions.
The technology has become reasonably common in Europe and Canada over the past several years. Now, Portland’s burgeoning collection of timber-framed projects makes our tree-rich state a national leader in a worldwide trend.
“It’s not an accident,” says Portland architect Thomas Robinson. “It’s in the culture, just waiting to be tapped.” Robinson’s firm, Lever Architecture, designed Albina Yard, just a mile from Carbon12’s site. A visit to Albina Yard (where Lever now has its headquarters) wowed even some of CLT’s Austrian pioneers: they’d never seen a CLT-framed building made with beautiful Douglas fir. For Robinson, building with Oregon’s signature tree is a kind of dream fulfilled: his great-grandfather’s Doug fir cabin on Cape Cod inspired him to become an architect.
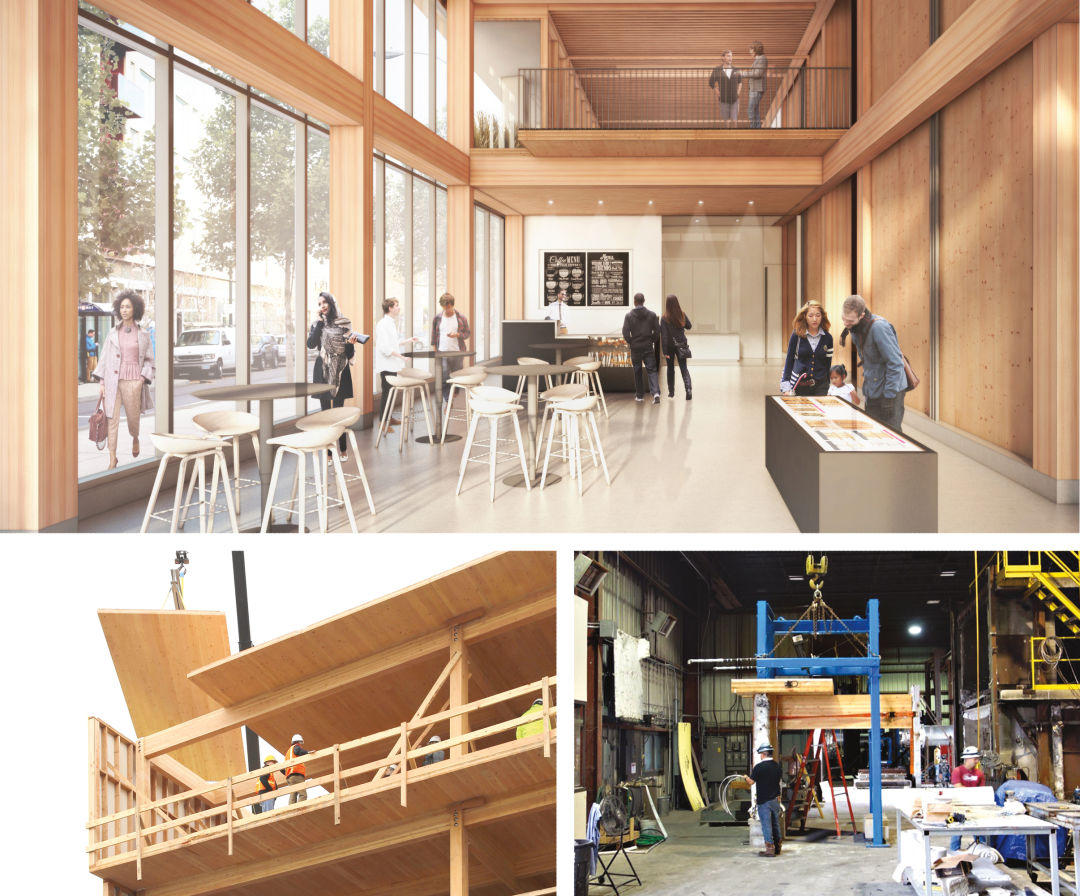
Clockwise from top: an interior rendering of Framework; a San Antonio workshop tests a section of cross-laminated timber, part of a process aimed at revising US building codes; Albina Yard, under construction
Image: Courtesy Lever Architecture
T
his spring construction begins on a 12-story, multiuse Pearl District building, designed by Lever, also called Framework (though unrelated to the other project of the same name). Last year, the Framework team, led by the local development firm Project, won a $1.5 million grant in the US Tall Wood Building Prize competition—sponsored by the US Department of Agriculture, the Softwood Lumber Board, and the Binational Softwood Lumber Council (the latter is a joint project of the US and Canadian governments)—to fund the approximately 25 tests necessary to prove CLT strong and fire-resistant enough to amend high-rise building codes to allow something so tall with wood as its primary structural element.
One test, for example, required a hunk of CLT to withstand a two-hour fire without sprinklers. The material passed: even if the exterior scorched, the core of CLT’s layered structured resisted the fire.
“It performed extremely well,” recalls Peter Dusicka, an associate professor in Portland State University’s Department of Civil & Environmental Engineering who oversaw some of the testing. “What’s exciting is that we’ve been limited to building out of timber up to a fairly limited height: four- or five-story buildings. Now I think we’re jumping ahead.”
The material’s early Portland adopters hope this new way to use wood will bring about changes beyond the city’s building boom. Projects like Lever’s Framework and Albina Yard source their cross-laminated timber from D.R. Johnson, a Southern Oregon supplier in the town of Riddle (population 1,185) that is first in the nation to manufacture the panels. That relationship could foretell a new economic connection between urban growth and Oregon’s staple rural industry.
Another plus: D.R. Johnson can custom-cut CLT panels to fit. “We can do all the fabrication at our plant before shipping,” says company president Valerie Johnson. “The panels are literally ready to just lift into place. That’s a major time and expense saver.” Johnson says that CLT now makes up about 20 percent of the family firm’s business but could account for 60 percent in five years.
For Kaiser—who says CLT was previously unknown to his bankers, investors, insurance agents, even subcontractors—every selling point of the material is a boon. And he can add one more marketing hook for future buyers of the building's condos: because timber-framed high-rises can weigh half as much (or less) as those supported by steel or concrete, they can move on shifting ground. With Oregonians fretting about the Cascadia Subduction Zone and a future megaquake, Kaiser can say this: “In a seismic event, I would bet this would be the safest building in the Northwest.”
Top Image: Lever Architecture's Albina Yard building (Courtesy Jeremy Bittermann)